

WESTMINSTER TOWER
Working on another unrelated project, Accent Services discovered an issue where hidden corrosion could lead to hazardous leaks, system failure and in an extreme case, the potential for an explosion on a Carrier 30GX chiller. The oil heater attached to the oil separator can be expected to need replacement several times during the serviceable lifetime of this chiller and it is in the re-lagging of the system after such maintenance that the potential for water ingress, that is impossible to detect visually, was found to occur.
Once alerted to this potential danger, Accent Services pulled up their historic customer database and found in the region of 20 Carrier 30GX chillers that they had installed, going back some twenty years or more. Even though some of these no longer had ongoing maintenance contacts with Accent, the team knew the only truly professional course of action from a health and safety standpoint, was to contact all these customers, both current and elapsed to inform them of the situation.
Calibre Building Services Limited manage Westminster Tower, a 14 storey office building on the capital’s Albert Embankment, serviced by two of the chillers in question. Accent put together a proposed schedule of works to investigate, assess and potentially repair/replace parts where necessary.
Investigation
Working on one chiller at a time and one circuit at a time, Accent would carry out an initial inspection to determine the level of corrosion if any, report their findings and make any recommendations moving forward. To carry out this inspection, the chiller was isolated at its incoming power supply, the discharge, motor cooling, oil feed and liquid line service valves were isolated, remaining refrigerant was recovered from the high side of the system to the evaporator, and the refrigerant pressure was lowered to 0.5 Bar. Only then could the visual CUI (Corrosion Under Insulation) inspection take place.
Once the lagging and oil heaters had been removed from the oil separators, it was clear to see significant corrosion with a large amount of pitting to the vessel mainly around the base of the shell; predominantly at the 6-8 o’clock position, where the oil heater pads were fitted as well as around the discharge pipe outlet connection.
Further investigation of the area around the vessel data plate found it to be heavily corroded. The data plate was spot welded to the vessel on each corner and as such had allowed moisture to collect underneath. Accent were in no doubt that the circuit should not be reinstated back into operation without an (NDT) Non Destructive Test carried out by an independent accredited API 510 Inspector using ultrasonic thickness testing in accordance with ISO 17020 to the oil separators.
The client’s decision
Seeing the results of the inspection and after consultation with Accent, Calibre elected to forego the NDT, deciding that the costs involved in further inspection coupled with the fact that there was a second chiller in the same condition, meant it made no financial sense to proceed with anything other than a complete replacement of all four oil separators across the two chillers.
Accent, promptly carried out this work and both chillers were again fully operational after four weeks on site from the date of the inspection.
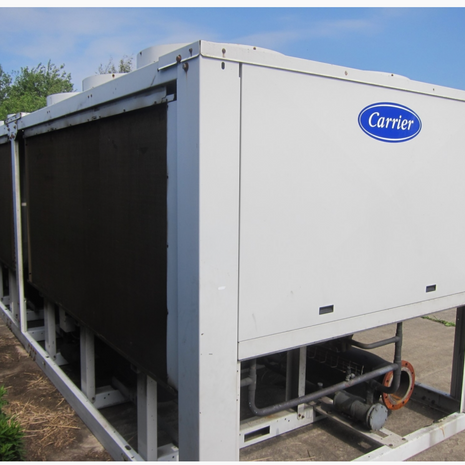
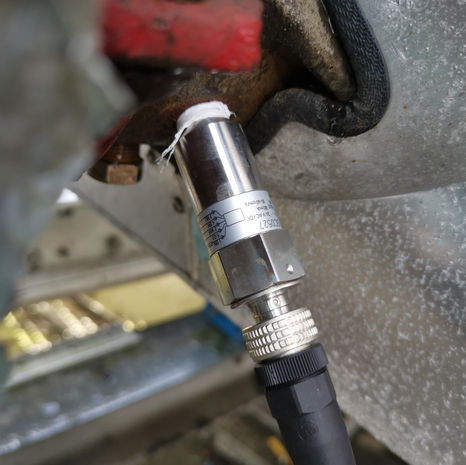
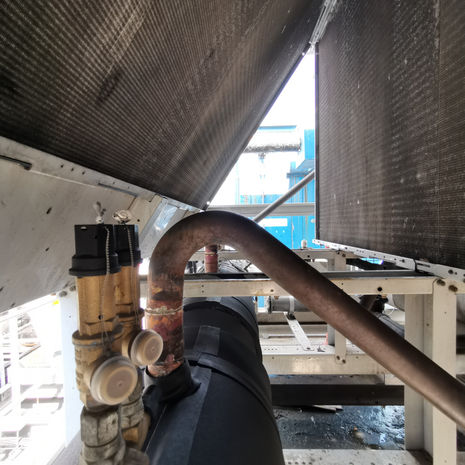


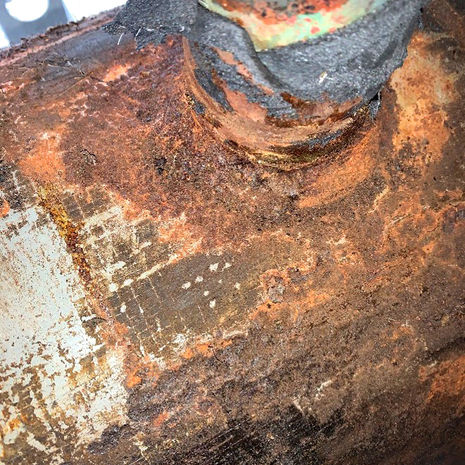
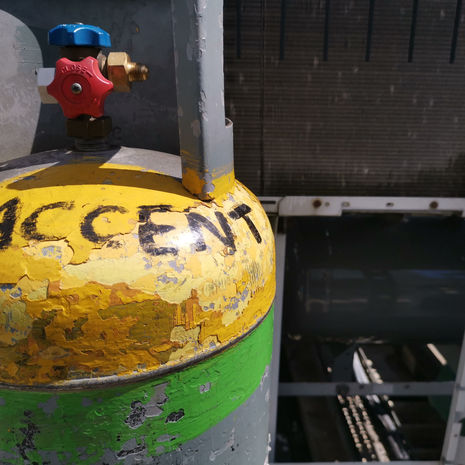




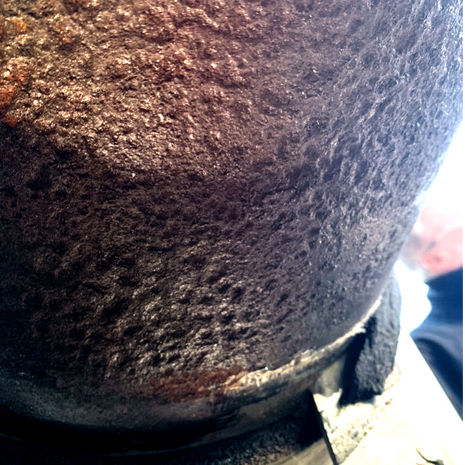